Setting the standard for water recovery and circular reuse in oat drink production
As plant-based drinks producers look to increase production in a global market predicted to rise to USD 71.46 billion by 2030 (Facts & Figures Research, 2023), innovative leaders in the industry are incorporating ‘sustainability as standard’ and building circularity into their expanding operations.
DATE 2024-08-07One such plant-based food and beverage producer in North America has made sustainability and operational circularity the foundations of their approach, driving day-to-day operations and strategic expansion.
Since 2000, the company has been solely focused on the manufacture and sale of organic food, with a focus on plant-based food and beverage. Two years earlier, the company had entered the oat drink business in response to booming consumer demand for plant-based products.
The venture was an opportunity to incorporate leading-edge design and innovation in engineering at a new plant to optimize process efficiency from the outset. And to do this, they worked with Alfa Laval, initially at the pilot scale, to fine-tune the design of the full-scale installation, which was commissioned and fully operational in 2020.
Alfa Laval’s AlfaVap evaporation systems are central to water-use optimization and energy efficiency at the plant. After mixing, cooking, and separating, the oat drink is concentrated with an AlfaVap evaporation system, which processes 16,000 kgs/hr of oat drink to produce 3,500 kgs/hr of 50-55% concentrate.
“The concentrated oat drink is sold in bulk to customers who reconstitute it, tailor it to their market specification, repackage it and sell it to consumers,” explains Ashok Shrivastava, Food Systems Service Sales with Alfa Laval. “Concentrating the product reduces the amount of packaging required and cuts all the costs and carbon emissions associated with transporting large volumes of liquid by a factor corresponding to the 78% lower volume.”
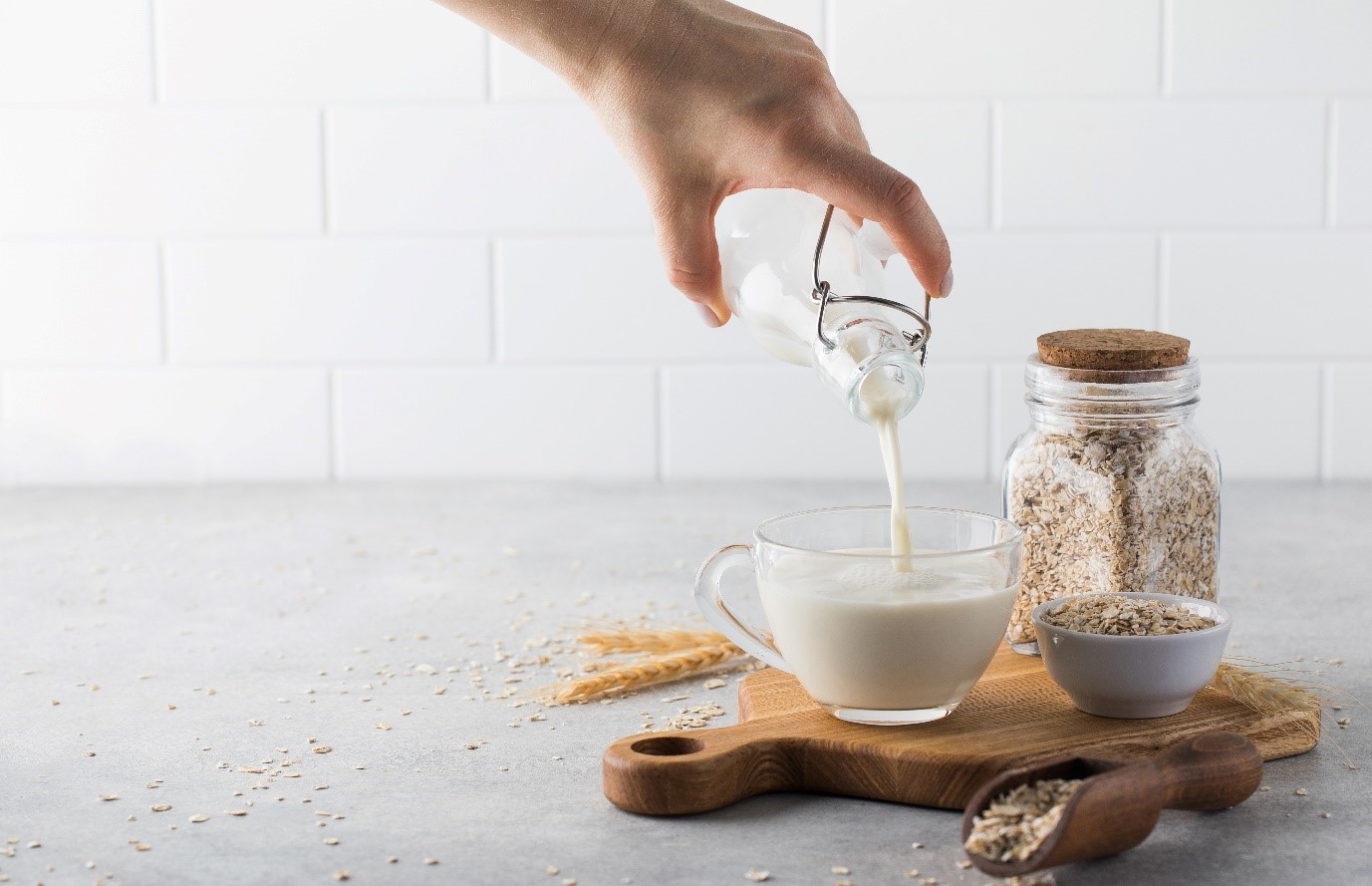
The AlfaVap evaporation system generates three distinct streams: firstly, concentrated oat drink; secondly, condensed live steam, also known as steam condensate; and finally, process condensate derived from the water vapor evaporated from the product. “Given the high water-intensity of the oat drink process, effective water management is crucial for maintaining control, optimizing production costs, and ensuring sustainable water consumption,” says Ashok.
Ultimately, the recovered condensate – water that can be treated and reused – amounts to 15,300 litres an hour: 8,000 litres of process condensate and 7,300 litres of steam condensate.
“The process is highly efficient,” says Ashok. “The steam is reused three times throughout the evaporation process, while the water or process condensate from each phase is returned for reuse in the first step of the mixing and cooking process of the oats. This is significant as the plant uses 8,000 litres of water per hour in this first step when it is working at full capacity.”
The 7,300 litres/hour of steam condensate from the first effect is also reused either for Cleaning-in-Place (CIP) or in the water feed for the boiler based on the conductivity and quality. Reusing the steam condensate, which emerges at 87°C, generates significant energy savings in the process.
“In the production cycle, all the steam and water are reused at least once, which reduces the amount of new water and energy needed for the boiler - both in the first step mixing and cooking process and for cleaning-in-place,” says Ashok. “Additionally, the CIP water is reused for three cycles before it is drained out and sent to the company’s own wastewater treatment plant, so the efficiency of CIP water use is also optimized.”
The company’s satisfaction with the operational efficiency of this plant was such that last year, they opened a second plant of the same design in a highly water scarce location.
“Water use and energy efficiency were the two key elements driving these projects,” says Ashok. “The customer wanted to incorporate as much circularity in water use as possible, which we have achieved. Also, by recycling the steam and vapours, there is a huge saving on energy as well.”
Fremhevede teknologier
CO2e savings
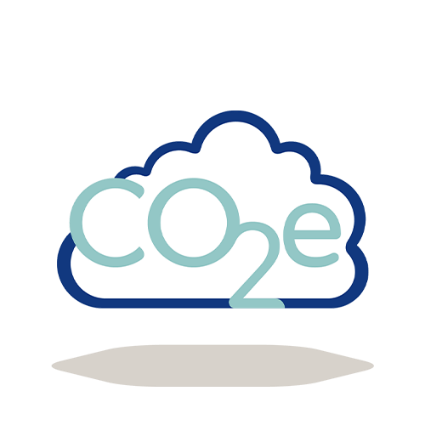
Reduction in carbon emissions corresponding to the 78% lower product volume during transportation
Energy savings
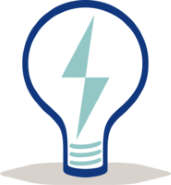
Optimized energy consumption thanks to energy efficiency and energy recovery
Water savings
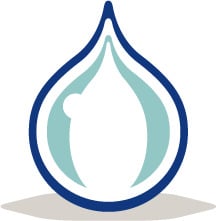
Water recovered and reused: 15,300 litres an hour